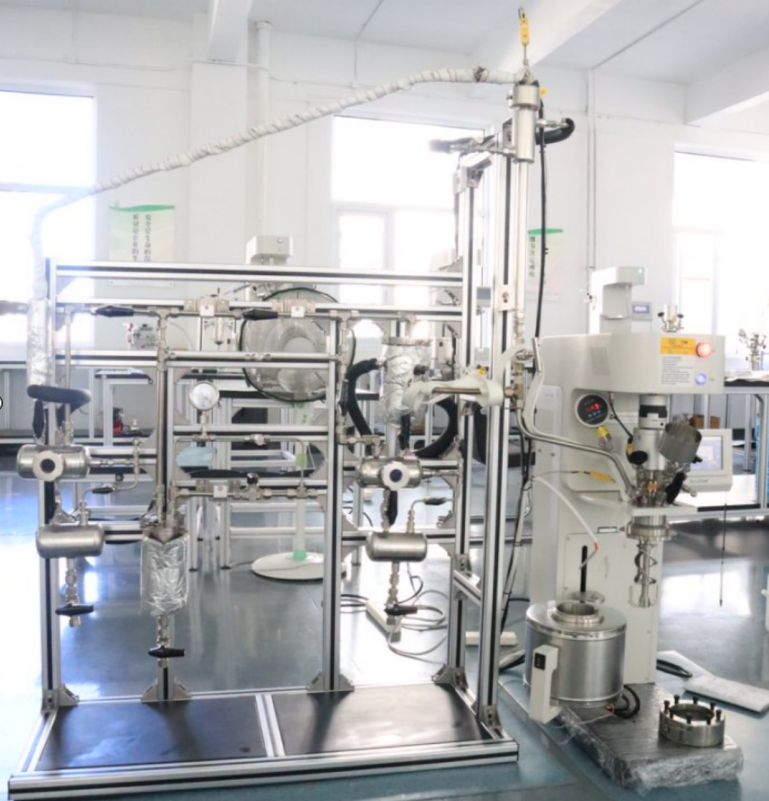
雙釜連續聚合反應裝置,高壓反應釜可串可并。是一種結合串聯反應釜設計的高效連續化生產系統,其核心功能在于通過多級反應過程優化聚合物合成工藝。
雙釜連續聚合反應裝置結構組成與設計特點:雙釜串聯架構,裝置由兩臺獨立森朗全自動反應釜組成,通過管道和泵送系統實現物料連續傳輸。
一臺反應釜通常用于單體預聚或初級聚合,第二反應釜完成深度聚合及產物調整。各釜體采用耐高溫、耐腐蝕材質(如316L不銹鋼),設計壓力可達100bar,溫度控制范圍50-250℃。攪拌系統采用雙層推進式結構,下層上翻、上層下壓的混合方式可提升反應均勻性。全自動連續流控制單元配置精密計量泵實現原料連續進料,同時通過真空管與真空機連接,實時排除氧氣防止聚合物氧化。釜間物料轉移采用密封式輸送,避免外部環境干擾,確保反應體系穩定性。關鍵控制系統溫控與壓力管理雙顯雙控溫控系統:主控模塊監測釜內物料溫度,輔控模塊調節加熱爐溫度,精度達±1℃。壓力傳感器實時監測,超壓時自動觸發安全聯鎖并切斷加熱。自動化操作界面7英寸真彩色觸控屏支持模塊化參數設置,具備數據采集、曲線生成及Excel導出功能。遠程控制通過RS485通訊接口實現,支持MODBUS RTU協議。雙釜連續聚合反應裝置,工藝優勢與應用領域效率與質量提升相比單釜間歇式反應器,連續化生產減少批次間隔時間,產能提升30%以上。通過消除氣泡單元(如消泡針與攪拌聯動設計)和真空脫氧技術,可顯著降低產物缺陷率。
雙釜連續聚合反應裝置,典型應用場景 高性能聚合物合成:如環烯烴共聚物(COC/COP)、高密度聚乙烯(HDPE)的連續制備。復雜反應體系:適用于茂金屬催化聚合、尼龍縮聚等需多階段控制的工藝58。安全與擴展性,多重安全保障:獨立機械升降模塊實現釜體快速分離,超溫/超壓報警系統與應急冷卻聯動。工藝兼容性:模塊化設計支持快速更換攪拌形式(錨式、渦輪式等)和加裝輔助設備(如在線分析儀)。此類裝置通過精準的過程控制和連續化生產模式,已成為高分子材料研發及工業化生產的關鍵設備,尤其在需要高純度、窄分子量分布的聚合物合成中表現突出。同時,北京世紀森朗關于連續聚合工藝,有雙釜連續聚合工藝,三釜連續聚合工藝,四釜連續聚合工藝等等。